Harvard startup designs medical efficiency, reduced footprint
As a medical logistician working in rural Liberia, Ian Speers grew frustrated: Boxes of single-use prefilled syringes – a staple in clinics and hospitals around the globe – were often inaccessible because they were bulky, expensive, and difficult to move.
“With each box, the wasted space and environmental impact became more and more apparent,” Speers recalled. “Prefilled syringes, like many medical devices and supplies, are not optimized for clinical or logistical use in many remote and low-resource settings. For instance, in the current traditional design of prefilled syringes, the extended plastic plunger rod wastes almost half the space in each box.”
The 2023 graduate of the Harvard T.H. Chan School of Public Health teamed up with two mechanical engineers, Robert Halvorsen and Ryan Stinebaugh, to develop a compact and resource-saving prefilled syringe that reduces packaging volumes by 40%, helping vaccines and other injections get to the most remote locations. The result is reduced packaging, shipping costs, and environmental impact – and more prefilled syringes in the hands of clinicians around the world.
Now, the three are looking to disrupt a global industry with their startup, Pacto Medical.
Seven billion prefilled syringes are used every year – many are simply saline solutions used to flush IV lines. With its smaller design, Pacto Medical can fit 7,000 more syringes on a pallet. Though there is no perfect way to measure the carbon footprint of such a sprawling supply chain, Pacto estimates that were all 7 billion syringes shipped from New York to London in containers just once, their product would save almost 6,000 tons of carbon emissions (equivalent to the carbon sequestered by a forest the size of 5,000 football fields) and almost 10 million pounds of packaging waste.
That’s all with one simple design change.
Pacto Medical is a member of the 2024 Climate Entrepreneurs Circle Cohort at the Harvard Innovation Labs, where it receives legal support and advising from established ventures at the intersection of medical supplies and climate. Last year, Pacto won an Ingenuity Award from the Harvard President’s Innovation Challenge.
Speers and Halvorsen sat down with Harvard’s Salata Institute for Climate and Sustainability to discuss their product and vision for a more sustainable medical-supply industry.
How did you develop this idea?
Ian Speers: Before coming to Harvard, I worked for a nonprofit managing public health programs, emergency responses, and doing a lot of work related to medical supply chains – mostly in Africa and the Middle East. We would accept high-quality donated products from around the world and redistribute them to areas that needed them urgently. I saw the challenge of getting products to the last mile, especially in low-resource settings with complicated supply chains. I quickly learned how supply-chain logistics could make or break what we were doing, whether it was running a field hospital or delivering a public health program. And I felt like that was often overlooked.
I’ve also been an EMT for over 10 years. In both situations, I saw the importance of prefilled syringes, how they allow a more sterile medication and better dosing accuracy. They’re a lot more convenient, they’re faster, and they create less waste because you’re not drawing out of a vial or ampoule.
Robert Halvorsen: The global reach potential of this product is huge, but the actual engineering challenge is relatively simple. It’s just two pieces of plastic that snap together. It’s a combination of elegance and simplicity with a far-reaching impact.
Where are you in the process of getting this to market?
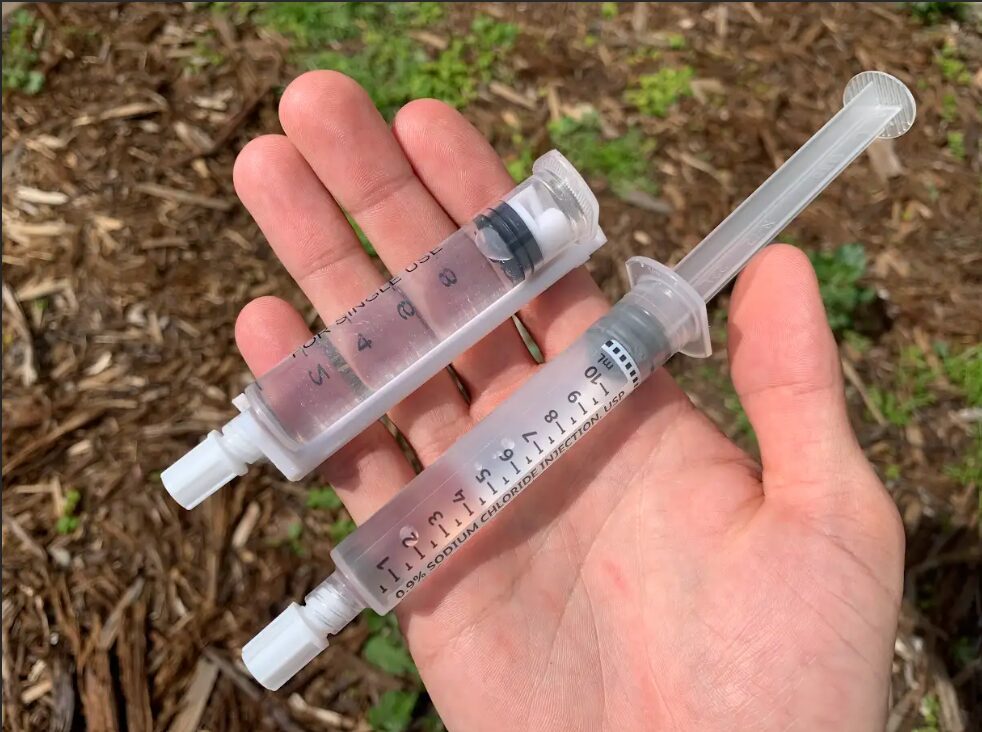
Robert Halvorsen [holding up a prefilled syringe]: This is a prototype with an off-the-shelf barrel and rubber stopper – these are industry standards. Our current plunger rod and stopper insert prototypes are 3D printed. The fidelity is nice, but they don’t have the mechanical properties that we would need to go to mass production. So, our current fundraising effort is to transition this 3D-printed prototype into an injection-molded part for rigorous engineering and user testing.
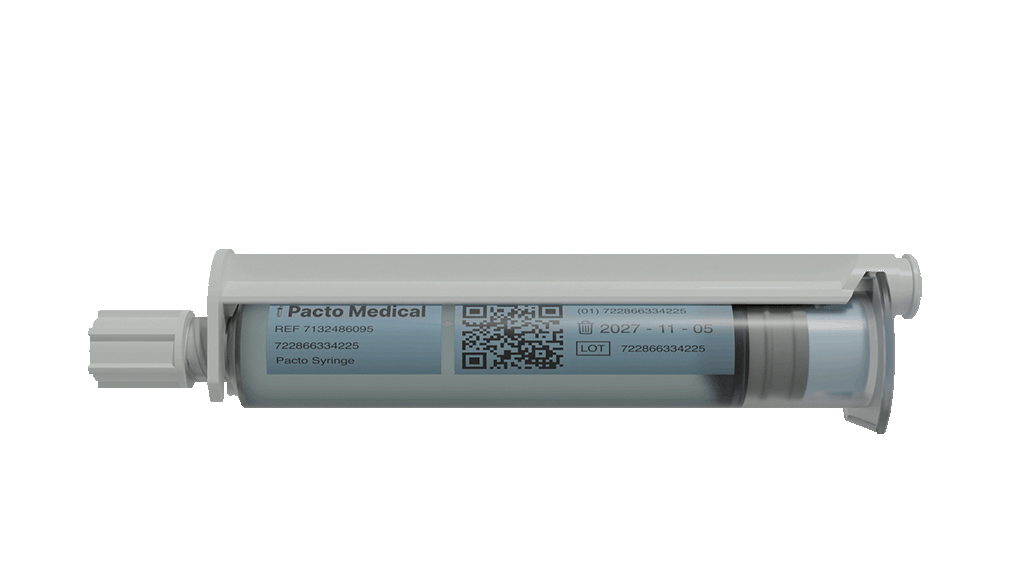
Does your product use less plastic than what’s on the market?
Robert Halvorsen:The product uses an equivalent amount of plastic, but the packaging is dramatically reduced. Every syringe is packaged in plastic wrapping. Because our wrapping is 40% shorter, that’s 40% less wrapping per unit. Usually these are packaged into a cardboard box. If you can fit more syringes per box, that’s a more efficient use of space. Then, from an environmental perspective, when these get shipped on trucks and planes and in containers, the reduced volume allows for more efficient transport and less carbon emissions.
How do you enter a market with established players who have all the manufacturing and distribution infrastructure already set up?
Robert Halvorsen: If we were to manufacture these ourselves and compete against [established firms], theirs would be cheaper because they make a billion and we would only make 100,000 or so of these. But if we’re able to reach the same scale, then the manufacturing costs would be roughly equivalent.
Ian Speers: That’s why we’re looking to partner with those existing players to reach scale faster – licensing or selling our proprietary components to a completed manufacturer who would then incorporate it into their designs. Then we could reach impact a lot faster.
You must be working on patents to protect yourselves.
Ian Speers: We’ve submitted U.S. utility and PCT patent applications and have made a number of claims to protect against infringement, not just on the exact current mechanism of attachment but a range of other iterations. We’ve thought of different ways you could theoretically do this and put them into that patent. In addition, we’ve been working on understanding what this means in terms of cost savings, in terms of environmental savings, how this would be implemented, and started user testing and trying to de-risk this as much as possible to make it a lot easier to work with us than against us. So, when we’re talking with stakeholders, we’re not just bringing a patent; we’re bringing close to two years of research on this concept.
We have some upcoming meetings with players in this field who are interested because it aligns with their goals and current initiatives to reduce costs, reduce environmental impacts, and improve access. They’re interested in seeing if there are opportunities to partner with us rather than having to start from scratch.
You are a member of the Harvard Innovation Labs 2024 Climate Entrepreneurs Circle Cohort. How has that helped you along the way?
Ian Speers: Yes, we do not have a ton of experience in the legal, patent, or corporate tax world. And the incredible advantage of working with the Harvard network is that we have received so much great feedback, advice, and guidance in these areas from countless experts. These folks really want us to succeed at what we do best, which is the engineering and the public health work. This support has also helped us file patents, a trademark, and much more without incurring any legal fees, which has been a huge advantage while we have been bootstrapping this company.